
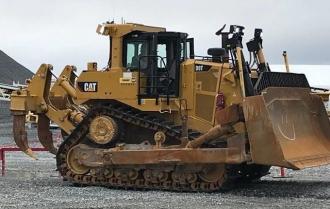
So, what happens if some mine sites are restricted to using relatively larger excavators (> 23 m 3 bucket) that are preferred for higher priority digging tasks? When can they avoid using their excavator? This paper explores multiple scenarios that have been designed and developed to simulate data results, which identify conditions in which the dozer side-cutting technique becomes more economically viable than excavator side-casting in terms of decreased unit cost per loose cubic metre. However, such excavator side-casting 'economic viability' assumes that smaller/ancillary type excavators are used (i.e.


Industry practices suggest the latter technique is less productive and economical than using an excavator. An alternative technique is to have the dozers 'side-cut' the material, which involves the dozers running parallel to the wall, digging out the material, and eventually rotating their blades to begin bulk pushing. Instead, an excavator can be used to side-cast this waste for the dozers to access. This is because dozers cannot physically get in behind the waste to begin the bulk pushing process. In open pit dozer bulk push operations, the material left resting against the highwall after blasting poses an issue. School of Mechanical and Mining Engineering, The University of Queensland, Australia The second D11 dozer is expected to be commissioned onsite at Blackwater in January.Dozer side-cutting' versus excavator side-casting on the highwall in dozer bulk push operations They are far, far more productive which reduces the cost per tonne.” “The best thing here is that it still handles like a U-Blade and can go into the same applications. National Group has lined up all six dozers to be fitted with the new Reclamation blade, or XU Blade, which takes the dozer from a 34 cu.meter blade, to a 42.2 cu.m, according to Garea. It’s a beefed-up frame that now does both.” Jason Garea, Mining Account Manager at Hastings Deering, said: “There is a single frame now used between both the D11 standard dozer and the carry dozer applications.

“We expect to lower maintenance and repair costs by up to 5% thanks to a new case and frame design, improved bearings, redesigned pin joints, and a 30% larger oil pan.” Caterpillar has developed this machine to ensure faster cycle times to produce more dirt at a lower cost per tonne, National Group added.Īckroyd said the contribution the dozers will add to production and efficiency will boost overall performance on site. In a Hastings Deering release in mid-December, National Group’s Managing Director, Mark Ackroyd, said: “The D11 is the industry’s best large dozer so it was a logical choice for us to bring in six new dozers to add to our expansive fleet.”Īlong with load sensing hydraulics reducing fuel burn, the new D11 will extend out component life from fuel burn to overhaul, according to the company. This would have seen the machine receive new load-sensing hydraulics and new drivetrain components among other additions.īMA’s Blackwater coal mine, in Queensland’s Bowen Basin, produced close to 2.1 Mt of coal in the most recent September quarter, according to BHP.
#Caterpillar d 11 dozer pushing coal update
While the specifics of this new dozer are not yet known, Cat did plan to launch an update to its D11 earlier this year. National Group secured the first of these dozers earlier this month from Cat dealer Hastings Deering as part of an order that would see six of these machines hauled by its National Heavy Haulage subsidiary, the company said. The first Caterpillar new generation D11 dozer in the world has started work at BHP Mitsubishi Alliance’s (BMA) Blackwater coal mine in Queensland, Australia, according to mining, resources, transport and logistics group National Group.
